Drain water tank/sediment from fuel filter
Check the fuel level in the service tank
Check the fuel level in the service tank.
Clean air filter
Check the lube oil level
Check the battery terminal
Check water level
Check tension of the belt/unusual noise
Check for leakages.
Check exhaust gas
General physical inspection for work loose parts.
Repeat the above tasks everyday to avoid system breakdown or failure.
Sunday, November 27, 2011
Friday, November 25, 2011
Preventive maintenance for forklift
You have a lot of money invested in your forklift. In order to protect that investment, perform preventive maintenance on your forklift regularly. Whether you or someone in your shop is performing your forklift maintenance or if you are having an outside company perform the maintenance on your forklift, it is good to know the procedure to be sure that your forklift is properly maintained.
Start the forklift and let it run briefly while you listen to the engine performance. Listen for any knocks or misses. Listen for any squealing caused by the belts. Then listen for any exhaust leaks. Drive the forklift forwards and backwards to check for any slips and to observe any possible wheel issues. Shut the engine off.
When performing preventative maintenance on your forklift, first check the horn, gauges, safety warning devices, cab lights, outside lights, back-up lights, and overhead guard for proper operation. Check for any burnt out bulbs and if any device still does not work, check the wiring and make repairs.
Next in your forklift preventative maintenance procedure is to check the battery compartment. Clean the battery terminal, battery cables and battery connectors. Open every cell cap and check the cells for proper fill levels and fill with water as needed. Apply protectant on the connectors to prevent corrosion. Leave the battery cables disconnected.
Drain the oil from your forklift. Change the oil filter, change the hydraulic filter, transmission filter, fuel filters, and the air filter. Prior to installing the new filters, use a permanent marker to write the date on the new filter. Check all fluid levels and fill as necessary. Check the anti-freeze in the cooling system.
Visually inspect the drive axle when you are underneath the machine. If there is a grease fitting, make sure to grease the drive axle.
Check the belts on the forklift engine. Check for cracks and frays on the belts.
Perform a visual check of the forklift's exhaust system. Look for any cracks or holes in the exhaust system.
Look at the tires on the forklift for any cracks or signs of excessive wear. On an air filled tire, check the tread. Check the differential fluid.
Check the clutch pedal on your forklift. Check the steering cylinder and the drag links. Check for any leaks or for any bends in the system.
Proceed to the hoist and look at the hydraulic lines for any leaks. If there are any leaks on the hydraulic system of your forklift, tighten the lines. If this does not correct the leaks, the fittings may need to be changed or an o-ring may need to be replaced.
While inspecting the hoist, look at the forks and mast to see if there are any visible cracks or chips. Look for any bowing or bends in the forks. Any of these should be noted on your checklist and flagged to the owner and operator as a potentially dangerous issue which needs to be further addressed.
Lubricate all the fittings on your forklift. This would include the hoist mechanism and tie-rod ends.
Checking the wheel bearings is listed on preventative maintenance checklists. However, this is normally done when replacing the brakes on the forklift. Unless there is some indication during the initial driving check out of the forklift that there may be an issue with the wheel bearings, it is not recommended to check the wheel bearings. More harm than good may be done when checking the wheel bearings.
Reconnect the battery cables and start the forklift again. Listen again for any unusual noises.
Lastly, a good preventative maintenance on your forklift will include some cleaning. Wipe down the forklift and use a spray cleaner to clean the forklift. Jeff recommends an oil based spray cleaner for the most effective cleaning of your forklift.
Always follow proper safety procedures when performing any maintenance on your forklift.
Start the forklift and let it run briefly while you listen to the engine performance. Listen for any knocks or misses. Listen for any squealing caused by the belts. Then listen for any exhaust leaks. Drive the forklift forwards and backwards to check for any slips and to observe any possible wheel issues. Shut the engine off.
When performing preventative maintenance on your forklift, first check the horn, gauges, safety warning devices, cab lights, outside lights, back-up lights, and overhead guard for proper operation. Check for any burnt out bulbs and if any device still does not work, check the wiring and make repairs.
Next in your forklift preventative maintenance procedure is to check the battery compartment. Clean the battery terminal, battery cables and battery connectors. Open every cell cap and check the cells for proper fill levels and fill with water as needed. Apply protectant on the connectors to prevent corrosion. Leave the battery cables disconnected.
Drain the oil from your forklift. Change the oil filter, change the hydraulic filter, transmission filter, fuel filters, and the air filter. Prior to installing the new filters, use a permanent marker to write the date on the new filter. Check all fluid levels and fill as necessary. Check the anti-freeze in the cooling system.
Visually inspect the drive axle when you are underneath the machine. If there is a grease fitting, make sure to grease the drive axle.
Check the belts on the forklift engine. Check for cracks and frays on the belts.
Perform a visual check of the forklift's exhaust system. Look for any cracks or holes in the exhaust system.
Look at the tires on the forklift for any cracks or signs of excessive wear. On an air filled tire, check the tread. Check the differential fluid.
Check the clutch pedal on your forklift. Check the steering cylinder and the drag links. Check for any leaks or for any bends in the system.
Proceed to the hoist and look at the hydraulic lines for any leaks. If there are any leaks on the hydraulic system of your forklift, tighten the lines. If this does not correct the leaks, the fittings may need to be changed or an o-ring may need to be replaced.
While inspecting the hoist, look at the forks and mast to see if there are any visible cracks or chips. Look for any bowing or bends in the forks. Any of these should be noted on your checklist and flagged to the owner and operator as a potentially dangerous issue which needs to be further addressed.
Lubricate all the fittings on your forklift. This would include the hoist mechanism and tie-rod ends.
Checking the wheel bearings is listed on preventative maintenance checklists. However, this is normally done when replacing the brakes on the forklift. Unless there is some indication during the initial driving check out of the forklift that there may be an issue with the wheel bearings, it is not recommended to check the wheel bearings. More harm than good may be done when checking the wheel bearings.
Reconnect the battery cables and start the forklift again. Listen again for any unusual noises.
Lastly, a good preventative maintenance on your forklift will include some cleaning. Wipe down the forklift and use a spray cleaner to clean the forklift. Jeff recommends an oil based spray cleaner for the most effective cleaning of your forklift.
Always follow proper safety procedures when performing any maintenance on your forklift.
Wednesday, November 23, 2011
TECHNOLOGY: PREVENTIVE MAINTENANCE CHECK LIST FOR KREIS DISSOL...
TECHNOLOGY: PREVENTIVE MAINTENANCE CHECK LIST FOR KREIS DISSOL...: To maintain a paint dissolver.here are weekly preventive maintenance check list to carry out: -inspect the wide v-belt for wear and tear. ...
TECHNOLOGY: PREVENTIVE MAINTENANCE CHECK LIST FOR KREIS DISSOL...
TECHNOLOGY: PREVENTIVE MAINTENANCE CHECK LIST FOR KREIS DISSOL...: To maintain a paint dissolver.here are weekly preventive maintenance check list to carry out: -inspect the wide v-belt for wear and tear. ...
PREVENTIVE MAINTENANCE CHECK LIST FOR KREIS DISSOLVER
To maintain a paint dissolver.here are weekly preventive maintenance check list to carry out:
-inspect the wide v-belt for wear and tear. -check all hydraulic pipe connections for leaks,hydraulic oil level and/make necessary correction.-inspect the mixing blade for looseness or wear.-empty the tray,clean bag collectors of the dust plant.-clean and retighten all electrical terminals.-retighten all bolts and nuts on the machine.
-inspect the wide v-belt for wear and tear. -check all hydraulic pipe connections for leaks,hydraulic oil level and/make necessary correction.-inspect the mixing blade for looseness or wear.-empty the tray,clean bag collectors of the dust plant.-clean and retighten all electrical terminals.-retighten all bolts and nuts on the machine.
Tuesday, November 22, 2011
DAILY PRE-OPERATION CHECK LIST ON FORKLIFT
daily pre-operation check list is a very important process in which a maintenance engineer must carry out in order to make equipment reliability possible to achieve
FOR A FORKLIFT WITH 3 TONS
Check the vehicle body
water leakage,loose parts,exterior damage
Check the tire pressure,wear or damage.
Check lamp condition,damaged lamps
Check the hydraulic oil level,check for oil contamination,consistency
Check the radiator coolant level,antifreeze equipment
check the brake fluid level.
Check the battery terminals
check the load handling system.
Hope this will go along way in maintaining your forklift
FOR A FORKLIFT WITH 3 TONS
Check the vehicle body
water leakage,loose parts,exterior damage
Check the tire pressure,wear or damage.
Check lamp condition,damaged lamps
Check the hydraulic oil level,check for oil contamination,consistency
Check the radiator coolant level,antifreeze equipment
check the brake fluid level.
Check the battery terminals
check the load handling system.
Hope this will go along way in maintaining your forklift
Friday, November 18, 2011
TECHNOLOGY: Maintenance Schedules and Documentation
TECHNOLOGY: Maintenance Schedules and Documentation: Complete,thorough,and current documentation is essential to an effective maintenance program.Whether you are performing preventive,predictiv...
Tuesday, November 8, 2011
TECHNOLOGY: SHAFT ALIGNMENT
TECHNOLOGY: SHAFT ALIGNMENT: Misalignment is a common and sometimes serious problem.Poor alignment can cause premature wear or failure of bearings,overheating of shaft c...
SHAFT ALIGNMENT
Misalignment is a common and sometimes serious problem.Poor alignment can cause premature wear or failure of bearings,overheating of shaft couplings,and,in extreme cases,cracked or broken shafts.The procedure for alignment depends on the type of equipment and its design.
Large vertical units,suspended from a thrust bearing in the motor or generator,require making the shaft plumb and the guide bearings concentric.
The lineshafts of vertical turbine pumps are held in alignment by lineshaft bearings in the pipe column.The proper alignment of the lineshaft depends on the proper assembly of the pipe column and the bearing retainers.Depending on the design,the pump motor to lineshaft coupling may be aligned by the face and rim method or the reverse indicator method.
Large vertical units,suspended from a thrust bearing in the motor or generator,require making the shaft plumb and the guide bearings concentric.
The lineshafts of vertical turbine pumps are held in alignment by lineshaft bearings in the pipe column.The proper alignment of the lineshaft depends on the proper assembly of the pipe column and the bearing retainers.Depending on the design,the pump motor to lineshaft coupling may be aligned by the face and rim method or the reverse indicator method.
Saturday, November 5, 2011
Turbine and pump maintenance
HYDRAULIC TURBINES.
Hydraulic turbines are classified as either reaction turbines or impulse turbines reffering to the hydraulic action by which the pressure or potential energy is converted to rotating or kinetic energy.The reaction turbines include the francis turbine and the propeller types,while thew impulse turbines are represented by the pelton type turbine.
Impulse turbines convert all available head into kinetic or velocity energy through using contracting nozzles.The jets of water from the nozzles act on the runner buckets to exert a force in the direction of flow.This force or impulse as it is referred to turns the turbine.Impulse turbines primarily are used for heads of 800feet or more although they are also used in some low-head applications.
A propeller turbine is similar in appearance to a boat propeller.Water is directed and controlled in much the same manner as with the francis turbine.A variation of the propeller turbine is the kaplan turbine which features adjustable blades that are pivoted to obtain the highest efficiency possible at any load.
Hydraulic turbines are classified as either reaction turbines or impulse turbines reffering to the hydraulic action by which the pressure or potential energy is converted to rotating or kinetic energy.The reaction turbines include the francis turbine and the propeller types,while thew impulse turbines are represented by the pelton type turbine.
Impulse turbines convert all available head into kinetic or velocity energy through using contracting nozzles.The jets of water from the nozzles act on the runner buckets to exert a force in the direction of flow.This force or impulse as it is referred to turns the turbine.Impulse turbines primarily are used for heads of 800feet or more although they are also used in some low-head applications.
A propeller turbine is similar in appearance to a boat propeller.Water is directed and controlled in much the same manner as with the francis turbine.A variation of the propeller turbine is the kaplan turbine which features adjustable blades that are pivoted to obtain the highest efficiency possible at any load.
Thursday, November 3, 2011
TECHNOLOGY: Maintenance Schedules and Documentation
TECHNOLOGY: Maintenance Schedules and Documentation: Complete,thorough,and current documentation is essential to an effective maintenance program.Whether you are performing preventive,predictiv...
Maintenance Schedules and Documentation
Complete,thorough,and current documentation is essential to an effective maintenance program.Whether you are performing preventive,predictive,or reliability centred maintenance,keeping track of equipment condition and maintenance performed or planned is critical.
Maintenance recommendations contained in this report should be used as the basis for establishing or refining a maintenance schedule.Recommendations can be converted into job plans or work orders in MAXIMO or another maintenance management system.Once these job plans and work orders are established,implementation of well executed predictive or RCM is possible.
The maintenance recordkeeping system must be kept current so that a complete maintenance history of each piece of equipment is available at all times.This is important for planning and conducting an ongoing maintenance program and provides documentation needed for the power O and M reviews.Regular maintenance and emergency maintenance must well be documented,as should special work done during overhauls and replacement.
Maintenance recommendations contained in this report should be used as the basis for establishing or refining a maintenance schedule.Recommendations can be converted into job plans or work orders in MAXIMO or another maintenance management system.Once these job plans and work orders are established,implementation of well executed predictive or RCM is possible.
The maintenance recordkeeping system must be kept current so that a complete maintenance history of each piece of equipment is available at all times.This is important for planning and conducting an ongoing maintenance program and provides documentation needed for the power O and M reviews.Regular maintenance and emergency maintenance must well be documented,as should special work done during overhauls and replacement.
Wednesday, November 2, 2011
TECHNOLOGY: Predictive maintenance of mechanical systems.
TECHNOLOGY: Predictive maintenance of mechanical systems.: predictive maintenance is a maintenance strategies carried out on mechanical equipments.it focuses on critical equipments of the systems. ...
Predictive maintenance of mechanical systems.
predictive maintenance is a maintenance strategies carried out on mechanical equipments.it focuses on critical equipments of the systems. Basically it deals with equipments monitoring on a daily basis.it uses accelerometer to read the vibration of the system.it is very easy to carry on but expensive.
TECHNOLOGY: GENERATOR MAINTENANCE SCHEDULING.
TECHNOLOGY: GENERATOR MAINTENANCE SCHEDULING.: A generator is an electromechanical device that converts mechanical energy to useful electrical. Generators varies in sizes and also varies ...
GENERATOR MAINTENANCE SCHEDULING.
A generator is an electromechanical device that converts mechanical energy to useful electrical. Generators varies in sizes and also varies in the power it generates.We also have the sound proof generators which reduces the noise to a low decibel of sound. The diesel generator is an example of critical equipments which needs to be maintained adequately for effective systems reliability.The basic preventive maintenance for the diesel generator is to service the generator every 250 hours of operation.
1-Drain the oil sump.2.change the oil filter.3.change the fuel filter.4.blow the air filter.
1-Drain the oil sump.2.change the oil filter.3.change the fuel filter.4.blow the air filter.
Tuesday, November 1, 2011
TECHNOLOGY: OVERHAULING OF MECHANICAL EQUIPMENTS.
TECHNOLOGY: OVERHAULING OF MECHANICAL EQUIPMENTS.: Overhauling, a technical term used in maintenance is defined as changing or replacement of main components of mechanical systems over a per...
OVERHAULING OF MECHANICAL EQUIPMENTS.
Overhauling, a technical term used in maintenance is defined as changing or replacement of main components of mechanical systems over a period of yearsi.e minimum of 5years.Here are parts needed to be overhauled in the following mechanical systems. Equiments partsoverhauled
generator crankshaft,piston. Forklift rockerarm,tapete. Compressor airvalve,piston. Hydraulic pump Gears.
generator crankshaft,piston. Forklift rockerarm,tapete. Compressor airvalve,piston. Hydraulic pump Gears.
TECHNOLOGY: TROUBLE SHOOTING OF A SIMPLE VAPOUR COMPRESSION RE...
TECHNOLOGY: TROUBLE SHOOTING OF A SIMPLE VAPOUR COMPRESSION RE...: WHAT IS A VAPOUR COMPRESSION REFRIGERATION SYSTEM? A vapour compression refrigerating system is an improved type of air refrigeration syste...
TROUBLE SHOOTING OF A SIMPLE VAPOUR COMPRESSION REFRIGERATION S YSTEM.
WHAT IS A VAPOUR COMPRESSION REFRIGERATION SYSTEM?
A vapour compression refrigerating system is an improved type of air refrigeration system in which a suitable working substance termed refrigerant is used.It condenses and evaporates at temperatures and pressures close to the atmospheric conditions.The refrigerants usually used for this purposes are ammonia,Carbon dioxide and sulphur dioxide.The refrigerant used does not leave the system but is circulated throughout the system.
TROUBLESHOOTING TECHNIQUES.
The first thing to check for is refrigerant leakages
Secondly check if the compressors,condensers and evaporators are working.
A vapour compression refrigerating system is an improved type of air refrigeration system in which a suitable working substance termed refrigerant is used.It condenses and evaporates at temperatures and pressures close to the atmospheric conditions.The refrigerants usually used for this purposes are ammonia,Carbon dioxide and sulphur dioxide.The refrigerant used does not leave the system but is circulated throughout the system.
TROUBLESHOOTING TECHNIQUES.
The first thing to check for is refrigerant leakages
Secondly check if the compressors,condensers and evaporators are working.
TECHNOLOGY: Troubleshooting of internal combustion engines.
TECHNOLOGY: Troubleshooting of internal combustion engines.: WHAT IS INTERNAL COMBUSTION ENGINES? Internal combustion engines are engines in which the combustion of air-fuel mixture takes place intern...
Troubleshooting of internal combustion engines.
WHAT IS INTERNAL COMBUSTION ENGINES?
Internal combustion engines are engines in which the combustion of air-fuel mixture takes place internally i.e in d combustion chamber.examples are the diesel generator,forklift engines.e.t.c.Troubleshooting is when a maintenance engineer or technician is trying to get a particular area where the problem is occuring.Troubleshooting requires the technical know how of the maintenance engineer. The first step to take when troubleshooting is to release air trapped in the combustion chamber.Second step is to check the airfilter,fuelfilter,battery terminals,oil filter.
Internal combustion engines are engines in which the combustion of air-fuel mixture takes place internally i.e in d combustion chamber.examples are the diesel generator,forklift engines.e.t.c.Troubleshooting is when a maintenance engineer or technician is trying to get a particular area where the problem is occuring.Troubleshooting requires the technical know how of the maintenance engineer. The first step to take when troubleshooting is to release air trapped in the combustion chamber.Second step is to check the airfilter,fuelfilter,battery terminals,oil filter.
Saturday, October 29, 2011
TECHNOLOGY: The Diesel generator set.
TECHNOLOGY: The Diesel generator set.: The packaged combination of a diesel engine, a generator and various ancillary devices (such as base, canopy, sound attenuation, control sys...
Saturday, October 22, 2011
express: SHAFT COUPLINGS
express: SHAFT COUPLINGS: Couplings are used to connect the shaft of a driver,such as a turbine or a motor,to the shaft of a driven machine,such as a pump or generato...
SHAFT COUPLINGS
Couplings are used to connect the shaft of a driver,such as a turbine or a motor,to the shaft of a driven machine,such as a pump or generator.There are basically two types of couplings;rigid and flexible.
Rigid couplings require precise alignment and most commonly are used in vertical units where the entire weight is supported by thrust bearings in the motor or generator.Flanged couplings are used on large,vertical units and consist of precisely machined flanges on each shaft connected by a series of coupling bolts around the perimeter of the flanges.
Flexible couplings are designed to accommodate slight misalignment between shafts and to some extent,dampen vibration.If properly aligned,most couplings should require very little maintenance outside of periodic inspection and in some cases lubrication.Over time,the alignment between the pump and its driver can deteriorate,increasing stress on the coupling which can lead to a shorter life.
Rigid couplings require precise alignment and most commonly are used in vertical units where the entire weight is supported by thrust bearings in the motor or generator.Flanged couplings are used on large,vertical units and consist of precisely machined flanges on each shaft connected by a series of coupling bolts around the perimeter of the flanges.
Flexible couplings are designed to accommodate slight misalignment between shafts and to some extent,dampen vibration.If properly aligned,most couplings should require very little maintenance outside of periodic inspection and in some cases lubrication.Over time,the alignment between the pump and its driver can deteriorate,increasing stress on the coupling which can lead to a shorter life.
Sunday, October 16, 2011
express: OIL AND LUBRICANTS.
express: OIL AND LUBRICANTS.: The primary purpose of a lubricant is to reduce friction and wear between two moving surfaces,but a lubricant also acts as a coolant,prevent...
express: OIL AND LUBRICANTS.
express: OIL AND LUBRICANTS.: The primary purpose of a lubricant is to reduce friction and wear between two moving surfaces,but a lubricant also acts as a coolant,prevent...
OIL AND LUBRICANTS.
The primary purpose of a lubricant is to reduce friction and wear between two moving surfaces,but a lubricant also acts as a coolant,prevents corrosion,and seals out dirt and other contaminants.In order for a lubricant to perform as intended,careful attention must be given to its selection and application as well as its condition while in use.
OIL LUBRICATION
Oil lubrication can take many forms- from a simple squirt oil can to a complex circulating system.Regardless of the method by which the oil is applied,the intent is the same,which is to keep a lubricant film between moving surfaces.
GREASE LUBRICATION
Grease is a lubricant consisting of a lubricating oil combined with a thickening agent.The base oil makes up 85-95 percent of the grease and performs the actual lubrication.
HYDRAULIC OIL.
The main purpose of a hydraulic oil is to transmit power,but it also must lubricate the components of the hydraulic system.In many systems,a lubrication oil such as turbine oil can be used as the hydraulic fluid.If the system uses a gear pump,operates at pressures less than 1000psi and has similar viscosity requirements,a turbine oil can function very well as hydraulic oil.
OIL LUBRICATION
Oil lubrication can take many forms- from a simple squirt oil can to a complex circulating system.Regardless of the method by which the oil is applied,the intent is the same,which is to keep a lubricant film between moving surfaces.
GREASE LUBRICATION
Grease is a lubricant consisting of a lubricating oil combined with a thickening agent.The base oil makes up 85-95 percent of the grease and performs the actual lubrication.
HYDRAULIC OIL.
The main purpose of a hydraulic oil is to transmit power,but it also must lubricate the components of the hydraulic system.In many systems,a lubrication oil such as turbine oil can be used as the hydraulic fluid.If the system uses a gear pump,operates at pressures less than 1000psi and has similar viscosity requirements,a turbine oil can function very well as hydraulic oil.
Wednesday, September 28, 2011
express: The Diesel generator set.
express: The Diesel generator set.: The packaged combination of a diesel engine, a generator and various ancillary devices (such as base, canopy, sound attenuation, control sys...
The Diesel generator set.
The packaged combination of a diesel engine, a generator and various ancillary devices (such as base, canopy, sound attenuation, control systems, circuit breakers, jacket water heaters and starting system) is referred to as a "generating set" or a "genset" for short.
Set sizes range from 8 to 30 kW (also 8 to 30 kVA single phase) for homes, small shops & offices with the larger industrial generators from 8 kW (11 kVA) up to 2,000 kW (2500 kVA three phase) used for large office complexes, factories. A 2,000 kW set can be housed in a 40 ft ISO container with fuel tank, controls, power distribution equipment and all other equipment needed to operate as a standalone power station or as a standby backup to grid power. These units, referred to as power modules are gensets on large triple axle trailers weighing 85,000 pounds (38,555 kg) or more. A combination of these modules are used for small power stations and these may use from one to 20 units per power section and these sections can be combined to involve hundreds of power modules. In these larger sizes the power module (engine and generator) are brought to site on trailers separately and are connected together with large cables and a control cable to form a complete synchronized power plant.
Diesel generators, sometimes as small as 200 kW (250 kVA) are widely used not only for emergency power, but also many have a secondary function of feeding power to utility grids either during peak periods, or periods when there is a shortage of large power generators.
Ships often also employ diesel generators, sometimes not only to provide auxiliary power for lights, fans, and winches, etc. but also indirectly for main propulsion. With electric propulsion the generators can be placed in a convenient position, to allow more cargo to be carried. Electric drives for ships were developed prior to WW I. Electric drives were specified in many warships built during WW II because manufacturing capacity for large reduction gears was in short supply, compared to capacity for manufacture of electrical equipment.[1] Such a diesel-electric arrangement is also used in some very large land vehicles such as railroad locomotives.
[edit] Generator Size
Generating sets are selected based on the Electrical load they are intended to supply, the electrical loads total characteristics (kWe, kVA, var's and Harmonic Content including starting currents (normally from motors) and non-linear loads. The expected duty, for example, emergency, prime or continuous power as well as environmental conditions such as altitude, temperature and emissions regulations must be taken into account as well.
[edit] Power plants – electrical "island" mode
One or more diesel generators operating without a connection to an electrical grid are referred to as operating in "Island Mode". In island mode, several parallel generators provide the advantages of redundancy and better efficiency at partial loads. The plant brings generator sets online and takes them off line depending on the demands of the system at a given time. An islanded power plant intended for primary power source of an isolated community ("Prime Power") will often have at least three diesel generators, any two of which are rated to carry the required load. Groups of up to 20 are not uncommon.
Generators can be electrically connected together through the process of synchronization. Synchronization involves matching voltage, frequency, and phase before connecting the generator to the system. Failure to synchronize before connection could cause a high current short-circuit or wear and tear on the generator and/or its switchgear. The synchronization process can be done automatically by an auto-synchronizer module. The auto-synchronizer will read the voltage, frequency and phase parameters from the generator and bus-bar voltages, while regulating the speed through the engine governor or ECM (Engine Control Module).
Load can be shared among parallel running generators through load sharing. Load sharing can be achieved by using droop speed control controlled by the frequency at the generator, while it constantly adjusts the engine fuel control to shift load to and from the remaining power sources. A diesel generator will take more load when the fuel supply to its combustion system is increased, while load is released if fuel supply is decreased.
[edit] Supporting main utility grids
In addition to their well known role as power supplies during power failures, diesel generator sets also routinely support main power grids worldwide in two distinct ways:
[edit] Peak lopping
Maximum demand tariffs in many areas encourage the use of diesels to come on at times of maximum demand. In Europe this is typically on winter weekdays early evening peak when cooking and lights are on as people come home—around 5:30–7:00 PM, whereas in the United States this is often in the summer to meet the air conditioning load.
[edit] Grid support
Emergency standby diesel generators, for example such as those used in hospitals, water plant, are, as a secondary function, widely used in the US and the UK (Short Term Operating Reserve) to support the respective national grids at times for a variety of reasons. In the UK for example, some 0.5 GWe of diesels are routinely used to support the National Grid, whose peak load is about 60 GW. These are sets in the size range 200 kW to 2 MW. This usually occurs during, for example, the sudden loss of a large conventional 660 MW plant, or a sudden unexpected rise in power demand eroding the normal spinning reserve available.[2]
This is extremely beneficial for both parties - the diesels have already been purchased for other reasons; but to be reliable need to be fully load tested. Grid paralleling is a convenient way of doing this. This method of operation is normally undertaken by a third party aggregator who manages the operation of the generators and the interaction with the system operator.
In this way the UK National Grid can call on about 2 GW of plant which is up and running in parallel as quickly as two minutes in some cases. This is far quicker than a base load power station which can take 12 hours from cold, and faster than a gas turbine, which can take several minutes. Whilst diesels are very expensive in fuel terms, they are only used a few hundred hours per year in this duty, and their availability can prevent the need for base load station running inefficiently at part load continuously. The diesel fuel used is fuel that would have been used in testing anyway. See Control of the National Grid, National Grid Reserve Service[3][4]
A similar system operates in France known as EJP, where at times of grid extrema special tariffs can mobilize at least 5 GW of diesel generating sets to become available.In this case, the diesels prime function is to feed power into the grid.[5]
During normal operation in synchronization with the electricity net powerplants are governed with a five percent droop speed control. This means the full load speed is 100% and the no load speed is 105%. This is required for the stable operation of the net without hunting and dropouts of power plants. Normally the changes in speed are minor. Adjustments in power output are made by slowly raising the droop curve by increasing the spring pressure on a centrifugal governor. Generally this is a basic system requirement for all powerplants because the older and newer plants have to be compatible in response to the instantaneous changes in frequency without depending on outside communication.[6]
[edit] Cost of generating electricity
See: Relative cost of electricity generated by different sources
[edit] Typical operating costs
Fuel consumption is the major portion of diesel plant owning and operating cost for power applications, whereas capital cost is the primary concern for backup generators. Specific consumption varies, but a modern diesel plant will consume between 0.28 and 0.4 litres[7][8] of fuel per kilowatt hour at the generator terminals.
However diesel engines can operate on a variety of different fuels, depending on configuration, though the eponymous diesel fuel derived from crude oil is most common. The engines can work with the full spectrum of crude oil distillates, from natural gas, alcohols, gasoline, wood gas to the fuel oils from diesel oil to residual fuels.[9] This is implemented by introducing gas with the intake air and using a small amount of diesel fuel for ignition. Conversion to 100% diesel fuel operation can be achieved instantaneously.[10]
* Fuel cost 11p - 16p/kWh (using red diesel at 40p/litre)
* lifetime engine maintenance about is 0.5p/kWh - 1.0p/kWh[4]
[edit] Typical costs of conversion to paralleling for grid operation
To be able to operate in parallel with the mains certain modifications are necessary which include the following:
* Approx. £3k to fit a PLC / Genest Controller to the set
* Paralleling and synchronising gear and G59 equipment including switchgear modifications (this allows grid connection) Approx £10k
* Tidying up set (noise, larger fuel tank) Approx another £5k
* So for a 1MW set…£13/kW
* 50 kW…maybe £260/kW
This capital cost of £13/kW - £260/kW is low compared to combined cycle gas turbines that cost £350/kW.[4]
[edit] Generator sizing and rating
[edit] Rating
Generators must be capable of delivering the power required for the hours per year anticipated by the designer to allow reliable operation and prevent damage. Typically a given set can deliver more power for fewer hours per year, or less power continuously. That is a standby set is only expected to give its peak output for a few hours per year, whereas a continuously running set, would be expected to give a somewhat lower output, but literally continuously, and both to have reasonable maintenance and reliability.
To meet the above criteria manufactures give each set a rating based on internationally agreed definitions.
These standard rating definitions are designed to allow correct machine selection and valid comparisons between manufacturers to prevent them from misstating the performance of their machines, and to guide designers.
Generator Rating Definitions[11]
Standby Rating based on Applicable for supplying emergency power for the duration of normal power interruption. No sustained overload capability is available for this rating. (Equivalent to Fuel Stop Power in accordance with ISO3046, AS2789, DIN6271 and BS5514). Nominally rated.
Typical application - emergency power plant in hospitals, offices, factories etc. Not connected to grid.
Prime (Unlimited Running Time) Rating: Should not be used for Construction Power applications. Output available with varying load for an unlimited time. Average power output is 70% of the prime rating. Typical peak demand 100% of prime-rated ekW with 10% of overload capability for emergency use for a maximum of 1 hour in 12. A 10% overload capability is available for limited time. (Equivalent to Prime Power in accordance with ISO8528 and Overload Power in accordance with ISO3046, AS2789, DIN6271, and BS5514). This rating is not applicable to all generator set models.
Typical application - where the generator is the sole source of power for say a remote mining or construction site, fairground, festival etc.
Base Load (Continuous) Rating based on: Applicable for supplying power continuously to a constant load up to the full output rating for unlimited hours. No sustained overload capability is available for this rating. Consult authorized distributor for rating. (Equivalent to Continuous Power in accordance with ISO8528, ISO3046, AS2789, DIN6271, and BS5514). This rating is not applicable to all generator set models
Typical application - a generator running a continuous unvarying load, or paralleled with the mains and continuously feeding power at the maximum permissible level 8760 hours per year. This also applies to sets used for peak shaving /grid support even though this may only occur for say 200 hour per year.
As an example if in a particular set the Standby Rating were 1000 kW, then a Prime Power rating might be 850 kW, and the Continuous Rating 800 kW. However these ratings vary according to manufacturer and should be taken from the manufacturer's data sheet.
Often a set might be given all three ratings stamped on the data plate, but sometimes it may have only a standby rating, or only a prime rating.
[edit] Sizing
Typically however it is the size of the maximum load that has to be connected and the acceptable maximum voltage drop which determines the set size, not the ratings themselves. If the set is required to start motors, then the set will have to be at least 3 times the largest motor, which is normally started first. This means it will be unlikely to operate at anywhere near the ratings of the chosen set.
Manufactures have sophisticated software that enables the correct choice of set for any given load combination. Sizing is based on what type of appliances, equipment, and devices that will be serviced by the generator.[12]
[edit] Correct Generator Installation
To ensure correct functioning, reliability and low maintenance costs generators must be installed correctly. To this end manufacturers provide detailed installation guidelines[13][14] covering such things as:
* Sizing and selection
* Electrical factors
* Cooling
Types of cooling
1. air cooling
2. water cooling
* Ventilation
* Fuel storage
* Noise
* Exhaust
* Starting systems
These are frequently ignored causing problems for users
[edit] Diesel engine damage due to misapplication or misuse of generating set
Diesel engines can suffer damage as a result of misapplication or misuse - namely internal glazing (occasionally referred to as bore glazing or piling) and carbon buildup. This is a common problem in generator sets caused by failure to follow application and operating guidelines. Ideally, diesel engines should be run at least 60-75% of their maximum rated load. Short periods of low load running are permissible providing the set is brought up to full load, or close to full load on a regular basis.
Internal glazing and carbon buildup is due to prolonged periods of running at low speeds and/or low loads. Such conditions may occur when an engine is left idling as a 'standby' generating unit, ready to run up when needed, (misuse); if the engine powering the set is over-powered (misapplication) for the load applied to it, causing the diesel unit to be under-loaded, or as is very often the case, when sets are started and run off load as a test (misuse).
Running an engine under low loads causes low cylinder pressures and consequent poor piston ring sealing since this relies on the gas pressure to force them against the oil film on the bores to form the seal. Low cylinder pressures causes poor combustion and resultant low combustion pressures and temperatures.
This poor combustion leads to soot formation and unburnt fuel residues which clogs and gums piston rings, which causes a further drop in sealing efficiency and exacerbates the initial low pressure. Glazing occurs when hot combustion gases blow past the now poorly-sealing piston rings, causing the lubricating oil on the cylinder walls to 'flash burn', creating an enamel-like glaze which smooths the bore and removes the effect of the intricate pattern of honing marks machined into the bore surface which are there to hold oil and return it to the crankcase via the scraper ring.
Hard carbon also forms from poor combustion and this is highly abrasive and scrapes the honing marks on the bores leading to bore polishing, which then leads to increased oil consumption (blue smoking) and yet further loss of pressure, since the oil film trapped in the honing marks is intended to maintain the piston seal and pressures.
Unburnt fuel then leaks past the piston rings and contaminates the lubricating oil. Poor combustion causes the injectors to become clogged with soot, causing further deterioration in combustion and black smoking.
The problem is increased further with the formation of acids in the engine oil caused by condensed water and combustion by-products which would normally boil off at higher temperatures. This acidic build-up in the lubricating oil causes slow but ultimately damaging wear to bearing surfaces.
This cycle of degradation means that the engine soon becomes irreversibly damaged and may not start at all and will no longer be able to reach full power when required.
Under-loaded running inevitably causes not only white smoke from unburnt fuel but over time will be joined by blue smoke of burnt lubricating oil leaking past the damaged piston rings, and black smoke caused by damaged injectors. This pollution is unacceptable to the authorities and neighbors.
Once glazing or carbon build up has occurred, it can only be cured by stripping down the engine and re-boring the cylinder bores, machining new honing marks and stripping, cleaning and de-cooking combustion chambers, fuel injector nozzles and valves. If detected in the early stages, running an engine at maximum load to raise the internal pressures and temperatures allows the piston rings to scrape glaze off the bores and allows carbon buildup to be burnt off. However, if glazing has progressed to the stage where the piston rings have seized into their grooves, this will not have any effect.
The situation can be prevented by carefully selecting the generator set in accordance with manufacturers printed guidelines.
For emergency only sets which are islanded, the emergency load is often only about 1/4 of the sets standby rating, this apparent over size being necessitated to be able to meet starting loads and minimizing starting voltage drop. Hence the available load is not usually enough for load testing and again engine damage will result if this us used as the weekly or monthly load test. This situation can be dealt with by hiring in a load bank for regular testing, or installing a permanent load bank. Both these options cost money in terms of engine wear and fuel use but are better than the alternative of under loading the engine. For remote locations a Salt water rheostat can be readily constructed.
Often the best solution in these cases will be to convert the set to parallel running and feed power into the grid, if available, once a month on load test, and or enrolling the set in utility Reserve Service type schemes, thereby gaining revenue from the fuel burnt.
Set sizes range from 8 to 30 kW (also 8 to 30 kVA single phase) for homes, small shops & offices with the larger industrial generators from 8 kW (11 kVA) up to 2,000 kW (2500 kVA three phase) used for large office complexes, factories. A 2,000 kW set can be housed in a 40 ft ISO container with fuel tank, controls, power distribution equipment and all other equipment needed to operate as a standalone power station or as a standby backup to grid power. These units, referred to as power modules are gensets on large triple axle trailers weighing 85,000 pounds (38,555 kg) or more. A combination of these modules are used for small power stations and these may use from one to 20 units per power section and these sections can be combined to involve hundreds of power modules. In these larger sizes the power module (engine and generator) are brought to site on trailers separately and are connected together with large cables and a control cable to form a complete synchronized power plant.
Diesel generators, sometimes as small as 200 kW (250 kVA) are widely used not only for emergency power, but also many have a secondary function of feeding power to utility grids either during peak periods, or periods when there is a shortage of large power generators.
Ships often also employ diesel generators, sometimes not only to provide auxiliary power for lights, fans, and winches, etc. but also indirectly for main propulsion. With electric propulsion the generators can be placed in a convenient position, to allow more cargo to be carried. Electric drives for ships were developed prior to WW I. Electric drives were specified in many warships built during WW II because manufacturing capacity for large reduction gears was in short supply, compared to capacity for manufacture of electrical equipment.[1] Such a diesel-electric arrangement is also used in some very large land vehicles such as railroad locomotives.
[edit] Generator Size
Generating sets are selected based on the Electrical load they are intended to supply, the electrical loads total characteristics (kWe, kVA, var's and Harmonic Content including starting currents (normally from motors) and non-linear loads. The expected duty, for example, emergency, prime or continuous power as well as environmental conditions such as altitude, temperature and emissions regulations must be taken into account as well.
[edit] Power plants – electrical "island" mode
One or more diesel generators operating without a connection to an electrical grid are referred to as operating in "Island Mode". In island mode, several parallel generators provide the advantages of redundancy and better efficiency at partial loads. The plant brings generator sets online and takes them off line depending on the demands of the system at a given time. An islanded power plant intended for primary power source of an isolated community ("Prime Power") will often have at least three diesel generators, any two of which are rated to carry the required load. Groups of up to 20 are not uncommon.
Generators can be electrically connected together through the process of synchronization. Synchronization involves matching voltage, frequency, and phase before connecting the generator to the system. Failure to synchronize before connection could cause a high current short-circuit or wear and tear on the generator and/or its switchgear. The synchronization process can be done automatically by an auto-synchronizer module. The auto-synchronizer will read the voltage, frequency and phase parameters from the generator and bus-bar voltages, while regulating the speed through the engine governor or ECM (Engine Control Module).
Load can be shared among parallel running generators through load sharing. Load sharing can be achieved by using droop speed control controlled by the frequency at the generator, while it constantly adjusts the engine fuel control to shift load to and from the remaining power sources. A diesel generator will take more load when the fuel supply to its combustion system is increased, while load is released if fuel supply is decreased.
[edit] Supporting main utility grids
In addition to their well known role as power supplies during power failures, diesel generator sets also routinely support main power grids worldwide in two distinct ways:
[edit] Peak lopping
Maximum demand tariffs in many areas encourage the use of diesels to come on at times of maximum demand. In Europe this is typically on winter weekdays early evening peak when cooking and lights are on as people come home—around 5:30–7:00 PM, whereas in the United States this is often in the summer to meet the air conditioning load.
[edit] Grid support
Emergency standby diesel generators, for example such as those used in hospitals, water plant, are, as a secondary function, widely used in the US and the UK (Short Term Operating Reserve) to support the respective national grids at times for a variety of reasons. In the UK for example, some 0.5 GWe of diesels are routinely used to support the National Grid, whose peak load is about 60 GW. These are sets in the size range 200 kW to 2 MW. This usually occurs during, for example, the sudden loss of a large conventional 660 MW plant, or a sudden unexpected rise in power demand eroding the normal spinning reserve available.[2]
This is extremely beneficial for both parties - the diesels have already been purchased for other reasons; but to be reliable need to be fully load tested. Grid paralleling is a convenient way of doing this. This method of operation is normally undertaken by a third party aggregator who manages the operation of the generators and the interaction with the system operator.
In this way the UK National Grid can call on about 2 GW of plant which is up and running in parallel as quickly as two minutes in some cases. This is far quicker than a base load power station which can take 12 hours from cold, and faster than a gas turbine, which can take several minutes. Whilst diesels are very expensive in fuel terms, they are only used a few hundred hours per year in this duty, and their availability can prevent the need for base load station running inefficiently at part load continuously. The diesel fuel used is fuel that would have been used in testing anyway. See Control of the National Grid, National Grid Reserve Service[3][4]
A similar system operates in France known as EJP, where at times of grid extrema special tariffs can mobilize at least 5 GW of diesel generating sets to become available.In this case, the diesels prime function is to feed power into the grid.[5]
During normal operation in synchronization with the electricity net powerplants are governed with a five percent droop speed control. This means the full load speed is 100% and the no load speed is 105%. This is required for the stable operation of the net without hunting and dropouts of power plants. Normally the changes in speed are minor. Adjustments in power output are made by slowly raising the droop curve by increasing the spring pressure on a centrifugal governor. Generally this is a basic system requirement for all powerplants because the older and newer plants have to be compatible in response to the instantaneous changes in frequency without depending on outside communication.[6]
[edit] Cost of generating electricity
See: Relative cost of electricity generated by different sources
[edit] Typical operating costs
Fuel consumption is the major portion of diesel plant owning and operating cost for power applications, whereas capital cost is the primary concern for backup generators. Specific consumption varies, but a modern diesel plant will consume between 0.28 and 0.4 litres[7][8] of fuel per kilowatt hour at the generator terminals.
However diesel engines can operate on a variety of different fuels, depending on configuration, though the eponymous diesel fuel derived from crude oil is most common. The engines can work with the full spectrum of crude oil distillates, from natural gas, alcohols, gasoline, wood gas to the fuel oils from diesel oil to residual fuels.[9] This is implemented by introducing gas with the intake air and using a small amount of diesel fuel for ignition. Conversion to 100% diesel fuel operation can be achieved instantaneously.[10]
* Fuel cost 11p - 16p/kWh (using red diesel at 40p/litre)
* lifetime engine maintenance about is 0.5p/kWh - 1.0p/kWh[4]
[edit] Typical costs of conversion to paralleling for grid operation
To be able to operate in parallel with the mains certain modifications are necessary which include the following:
* Approx. £3k to fit a PLC / Genest Controller to the set
* Paralleling and synchronising gear and G59 equipment including switchgear modifications (this allows grid connection) Approx £10k
* Tidying up set (noise, larger fuel tank) Approx another £5k
* So for a 1MW set…£13/kW
* 50 kW…maybe £260/kW
This capital cost of £13/kW - £260/kW is low compared to combined cycle gas turbines that cost £350/kW.[4]
[edit] Generator sizing and rating
[edit] Rating
Generators must be capable of delivering the power required for the hours per year anticipated by the designer to allow reliable operation and prevent damage. Typically a given set can deliver more power for fewer hours per year, or less power continuously. That is a standby set is only expected to give its peak output for a few hours per year, whereas a continuously running set, would be expected to give a somewhat lower output, but literally continuously, and both to have reasonable maintenance and reliability.
To meet the above criteria manufactures give each set a rating based on internationally agreed definitions.
These standard rating definitions are designed to allow correct machine selection and valid comparisons between manufacturers to prevent them from misstating the performance of their machines, and to guide designers.
Generator Rating Definitions[11]
Standby Rating based on Applicable for supplying emergency power for the duration of normal power interruption. No sustained overload capability is available for this rating. (Equivalent to Fuel Stop Power in accordance with ISO3046, AS2789, DIN6271 and BS5514). Nominally rated.
Typical application - emergency power plant in hospitals, offices, factories etc. Not connected to grid.
Prime (Unlimited Running Time) Rating: Should not be used for Construction Power applications. Output available with varying load for an unlimited time. Average power output is 70% of the prime rating. Typical peak demand 100% of prime-rated ekW with 10% of overload capability for emergency use for a maximum of 1 hour in 12. A 10% overload capability is available for limited time. (Equivalent to Prime Power in accordance with ISO8528 and Overload Power in accordance with ISO3046, AS2789, DIN6271, and BS5514). This rating is not applicable to all generator set models.
Typical application - where the generator is the sole source of power for say a remote mining or construction site, fairground, festival etc.
Base Load (Continuous) Rating based on: Applicable for supplying power continuously to a constant load up to the full output rating for unlimited hours. No sustained overload capability is available for this rating. Consult authorized distributor for rating. (Equivalent to Continuous Power in accordance with ISO8528, ISO3046, AS2789, DIN6271, and BS5514). This rating is not applicable to all generator set models
Typical application - a generator running a continuous unvarying load, or paralleled with the mains and continuously feeding power at the maximum permissible level 8760 hours per year. This also applies to sets used for peak shaving /grid support even though this may only occur for say 200 hour per year.
As an example if in a particular set the Standby Rating were 1000 kW, then a Prime Power rating might be 850 kW, and the Continuous Rating 800 kW. However these ratings vary according to manufacturer and should be taken from the manufacturer's data sheet.
Often a set might be given all three ratings stamped on the data plate, but sometimes it may have only a standby rating, or only a prime rating.
[edit] Sizing
Typically however it is the size of the maximum load that has to be connected and the acceptable maximum voltage drop which determines the set size, not the ratings themselves. If the set is required to start motors, then the set will have to be at least 3 times the largest motor, which is normally started first. This means it will be unlikely to operate at anywhere near the ratings of the chosen set.
Manufactures have sophisticated software that enables the correct choice of set for any given load combination. Sizing is based on what type of appliances, equipment, and devices that will be serviced by the generator.[12]
[edit] Correct Generator Installation
To ensure correct functioning, reliability and low maintenance costs generators must be installed correctly. To this end manufacturers provide detailed installation guidelines[13][14] covering such things as:
* Sizing and selection
* Electrical factors
* Cooling
Types of cooling
1. air cooling
2. water cooling
* Ventilation
* Fuel storage
* Noise
* Exhaust
* Starting systems
These are frequently ignored causing problems for users
[edit] Diesel engine damage due to misapplication or misuse of generating set
Diesel engines can suffer damage as a result of misapplication or misuse - namely internal glazing (occasionally referred to as bore glazing or piling) and carbon buildup. This is a common problem in generator sets caused by failure to follow application and operating guidelines. Ideally, diesel engines should be run at least 60-75% of their maximum rated load. Short periods of low load running are permissible providing the set is brought up to full load, or close to full load on a regular basis.
Internal glazing and carbon buildup is due to prolonged periods of running at low speeds and/or low loads. Such conditions may occur when an engine is left idling as a 'standby' generating unit, ready to run up when needed, (misuse); if the engine powering the set is over-powered (misapplication) for the load applied to it, causing the diesel unit to be under-loaded, or as is very often the case, when sets are started and run off load as a test (misuse).
Running an engine under low loads causes low cylinder pressures and consequent poor piston ring sealing since this relies on the gas pressure to force them against the oil film on the bores to form the seal. Low cylinder pressures causes poor combustion and resultant low combustion pressures and temperatures.
This poor combustion leads to soot formation and unburnt fuel residues which clogs and gums piston rings, which causes a further drop in sealing efficiency and exacerbates the initial low pressure. Glazing occurs when hot combustion gases blow past the now poorly-sealing piston rings, causing the lubricating oil on the cylinder walls to 'flash burn', creating an enamel-like glaze which smooths the bore and removes the effect of the intricate pattern of honing marks machined into the bore surface which are there to hold oil and return it to the crankcase via the scraper ring.
Hard carbon also forms from poor combustion and this is highly abrasive and scrapes the honing marks on the bores leading to bore polishing, which then leads to increased oil consumption (blue smoking) and yet further loss of pressure, since the oil film trapped in the honing marks is intended to maintain the piston seal and pressures.
Unburnt fuel then leaks past the piston rings and contaminates the lubricating oil. Poor combustion causes the injectors to become clogged with soot, causing further deterioration in combustion and black smoking.
The problem is increased further with the formation of acids in the engine oil caused by condensed water and combustion by-products which would normally boil off at higher temperatures. This acidic build-up in the lubricating oil causes slow but ultimately damaging wear to bearing surfaces.
This cycle of degradation means that the engine soon becomes irreversibly damaged and may not start at all and will no longer be able to reach full power when required.
Under-loaded running inevitably causes not only white smoke from unburnt fuel but over time will be joined by blue smoke of burnt lubricating oil leaking past the damaged piston rings, and black smoke caused by damaged injectors. This pollution is unacceptable to the authorities and neighbors.
Once glazing or carbon build up has occurred, it can only be cured by stripping down the engine and re-boring the cylinder bores, machining new honing marks and stripping, cleaning and de-cooking combustion chambers, fuel injector nozzles and valves. If detected in the early stages, running an engine at maximum load to raise the internal pressures and temperatures allows the piston rings to scrape glaze off the bores and allows carbon buildup to be burnt off. However, if glazing has progressed to the stage where the piston rings have seized into their grooves, this will not have any effect.
The situation can be prevented by carefully selecting the generator set in accordance with manufacturers printed guidelines.
For emergency only sets which are islanded, the emergency load is often only about 1/4 of the sets standby rating, this apparent over size being necessitated to be able to meet starting loads and minimizing starting voltage drop. Hence the available load is not usually enough for load testing and again engine damage will result if this us used as the weekly or monthly load test. This situation can be dealt with by hiring in a load bank for regular testing, or installing a permanent load bank. Both these options cost money in terms of engine wear and fuel use but are better than the alternative of under loading the engine. For remote locations a Salt water rheostat can be readily constructed.
Often the best solution in these cases will be to convert the set to parallel running and feed power into the grid, if available, once a month on load test, and or enrolling the set in utility Reserve Service type schemes, thereby gaining revenue from the fuel burnt.
Saturday, September 10, 2011
VIBRATION MONITORING AND ANALYSIS OF MECHANICAL SYSTEMS.
Vibration monitoring and analysis can be a useful part of a preventive or predictive maintenance program.There are a variety of vibration monitoring systems available.Some use permanently mounted sensors to continually monitor vibration levels,while other systems require readings to be taken periodically with handheld sensors.The type of system used depends on the equipment being monitored.The maintenance supervisor should compare the potential benefits of a vibration monitoring system,such as preventing damage and reducing outages,to the overall cost before deciding which system to use or whether to use any system at all.
PROXIMITY PROBE SYSTEMS.
A proximity probe is a non contacting type sensor which provides a direct current voltage directly proportional to shaft position relative to the probe.In a hydroelectic power plant or a large pumping plant,proximity probes are used to measure the main shaft runout on the turbine/generator or pump/motor
ACCELEROMETER SYSTEMS.
There is a number of accelerometer based vibration monitoring systems available,varying greatly in complexity and capability.Accelerometers are lightweight vibration sensors that,as the name implies,provide an electrical output proportional to the acceleration of the vibration of the machine being checked.
PROXIMITY PROBE SYSTEMS.
A proximity probe is a non contacting type sensor which provides a direct current voltage directly proportional to shaft position relative to the probe.In a hydroelectic power plant or a large pumping plant,proximity probes are used to measure the main shaft runout on the turbine/generator or pump/motor
ACCELEROMETER SYSTEMS.
There is a number of accelerometer based vibration monitoring systems available,varying greatly in complexity and capability.Accelerometers are lightweight vibration sensors that,as the name implies,provide an electrical output proportional to the acceleration of the vibration of the machine being checked.
Wednesday, September 7, 2011
express: OPERATION OF A WATER CHILLER
express: OPERATION OF A WATER CHILLER: The heated cooling agent steam is sucked out of the evaporator by the compressor and is compressed to the condensation pressure.The overheat...
OPERATION OF A WATER CHILLER
The heated cooling agent steam is sucked out of the evaporator by the compressor and is compressed to the condensation pressure.The overheated gas flows from the compressor into the aircooled condenser.In the condenser the cooling agent is cooled down by the air to such an extent,that it changes from gas to liquid. It flows on into the collector through the filter dryer and the inspection glass to the thermally controlled expansion valve.From here it flows as expanded cooling agent liquid to the non circulating water cooler.Here the cooling agent evaporates.The amount of heat required for this evaporation is taken from the circulating water and so the cycle can start a new.
In the suction pipe between evaporator and compressor there is a fluid absorber.At standstill of the plant,drops,which are not evaporated in the evaporator,seperate in the fluid absorber.
When starting the compressor,this fluid is sucked through the suction pipe.Thus a suction of too much cooling agent at starting the compressor,which could cause trouble,is prevented.
Tuesday, September 6, 2011
express: Daily checklist and maintenance on a diesel genera...
express: Daily checklist and maintenance on a diesel genera...: Drain water sediment from fuel tank/fuel filter Check the fuel level in the service tank Clean air filter Check the lube oil level Check the...
Daily checklist and maintenance on a diesel generator set
Drain water sediment from fuel tank/fuel filter
Check the fuel level in the service tank
Clean air filter
Check the lube oil level
Check the battery terminal
Check the water level
Check the tension of the belt/unusual noise
Check for leakages[oil,water,coolant]
Check exhaust gas
General physical inspection for work loose parts.
WITH THESE ABOVE DAILY CHECKLISTS,PROBLEMS,MAINTENANCE COSTS,WILL BE MINIMISED,AND THE SYSTEM RELIABILITY WILL INCREASE.
THANKS FOR READING.
Sunday, September 4, 2011
MAINTENANCE OF AIR COMPRESSORS
Air compressors are a common piece of equipment found in most pumping plants and maintenance shops.There are a number of different types of compressors available,but the two most common types which are the reciprocating and the rotary screw compressors.
RECIPROCATING COMPRESSOR.
A reciprocating compressor compresses air in a cylinder,against a cylinder head,by a reciprocating piston.
MAINTENANCE SCHEDULING
LUBRICATION
WEEKLY- Check that oil or grease cups are full and that crank case oil is at proper level.Replace or add the correct lubricant to bring to proper levels in crankcase or oil reservoir.
ANNUAL- Clean oil or grease cups and piping.Check condition of lubricant and change if required.
PACKING GLAND.
WEEKLY- Check for excessive leakage and scoring on piston rod.Adjust packing as necessary.
ANNUAL- Replace packing as necessary.
CYLINDER
Not scheduled- Check cylinder walls for wear and scoring.
PISTON
Not scheduled-Check piston for wear. Check clearance with micrometer.Examine rings for tightness and fits.
CONNECTING ROD
Not scheduled- Check for distortion or bending.Check bearing bolts and nuts for damage and replace as required.
Thursday, September 1, 2011
express: MAINTENANCE OF HYDRAULIC SYSTEMS
express: MAINTENANCE OF HYDRAULIC SYSTEMS: The right way to perform maintenance on a hydraulic system utilizing the Maintenance Best Practices
Most companies spend a lot of money t...
Most companies spend a lot of money t...
MAINTENANCE OF HYDRAULIC SYSTEMS
The right way to perform maintenance on a hydraulic system utilizing the Maintenance Best Practices
Most companies spend a lot of money training their maintenance personnel to troubleshoot a hydraulic system. If we focused on preventing system failure then we could spend less time and money on troubleshooting a hydraulic system. We normally accept hydraulic system failure rather than deciding not to accept hydraulic failure as the norm. Let’s spend the time and money to eliminate hydraulic failure rather than preparing for failure. I worked for Kendall Company in the 1980’s and we changed our focus from reactive to proactive maintenance on our hydraulic systems and thus eliminating unscheduled hydraulic failure. We will talk about the right way to perform maintenance on a hydraulic system utilizing the Maintenance Best Practices.
Lack of maintenance of hydraulic systems is the leading cause of component and system failure yet most maintenance personnel don’t understand proper maintenance techniques of a hydraulic system. The basic foundation to perform proper maintenance on a hydraulic system has two areas of concern. The first area is Preventive Maintenance which is key to the success of any maintenance program whether in hydraulics or any equipment which we need reliability. The second area is corrective maintenance, which in many cases can cause additional hydraulic component failure when it is not performed to standard.
Oil Pump
Preventive Maintenance
Preventive Maintenance of a hydraulic system is very basic and simple and if followed properly can eliminate most hydraulic component failure. Preventive Maintenance is a discipline and must be followed as such in order to obtain results. We must view a PM program as a performance oriented and not activity oriented. Many organizations have good PM procedures but do not require maintenance personnel to follow them or hold them accountable for the proper execution of these procedures. In order to develop a preventive maintenance program for your system you must follow these steps:
1st: Identify the system operating condition.
a. Does the system operate 24 hours a day, 7 days a week?
b. Does the system operate at maximum flow and pressure 70% or better during operation?
c. Is the system located in a dirty or hot environment?
2nd: What requirements does the Equipment Manufacturer state for Preventive Maintenance on the hydraulic system?
3rd: What requirements and operating parameters does the component manufacturer state concerning the hydraulic fluid ISO particulate?
4th: What requirements and operating parameters does the filter company state concerning their filters ability to meet this requirement?
5th: What equipment history is available to verify the above procedures for the hydraulic system?
As in all Preventive Maintenance Programs we must write procedures required for each PM Task. Steps or procedures must be written for each task and they must be accurate and understandable by all maintenance personnel from entry level to master.
Preventive Maintenance procedures must be a part of the PM Job Plan which includes:
* Tools or special equipment required performing the task.
* Parts or material required performing the procedure with store room number.
* Safety precautions for this procedure.
* Environmental concerns or potential hazards.
PM Procedures for Hydraulic Systems
A list of Preventive Maintenance Task for a Hydraulic System could be:
1. Change the (could be the return or pressure filter) hydraulic filter.
2. Obtain a hydraulic fluid sample.
3. Filter hydraulic fluid.
4. Check hydraulic actuators.
5. Clean the inside of a hydraulic reservoir.
6. Clean the outside of a hydraulic reservoir.
7. Check and record hydraulic pressures.
8. Check and record pump flow.
9. Check hydraulic hoses, tubing and fittings.
10. Check and record voltage reading to proportional or servo valves.
11. Check and record vacuum on the suction side of the pump.
12. Check and record amperage on the main pump motor.
13. Check machine cycle time and record.
Preventive Maintenance is the core support that a hydraulic system must have in order to maximize component and life and reduce system failure. Preventive Maintenance procedures that are properly written and followed properly will allow equipment to operate to its full potential and life cycle. Preventive Maintenance allows a maintenance department to control a hydraulic system rather than the system controlling the maintenance department. We must control a hydraulic system by telling it when we will perform maintenance on it and how much money we will spend on the maintenance for the system. Most companies allow the hydraulic system to control the maintenance on them, at a much higher cost.
In order to validate your preventive maintenance procedures you must have a good understanding and knowledge of “Best Maintenance Practices” for hydraulic systems. We will convey these practices to you.
Wednesday, August 31, 2011
express: TYPES OF MAINTAINENANCE FOR EFFECTIVE EQUIPMENT RE...
express: TYPES OF MAINTAINENANCE FOR EFFECTIVE EQUIPMENT RE...: PREVENTIVE MAINTENANCE: I s the practice of maintaining equipment on a regular schedule based on elapsed time or meter readings. Its aim is ...
TYPES OF MAINTAINENANCE FOR EFFECTIVE EQUIPMENT RELIABILITY
PREVENTIVE MAINTENANCE: Is the practice of maintaining equipment on a regular schedule based on elapsed time or meter readings. Its aim is to prevent maintenance problems or failures before they take place by following routine and comprehensive maintenance procedures.Here are the advantages of Preventive maintenance
-It is predictable,making budgeting,planning and resource levelling possible
- When properly practiced,it generally prevents most major problems,thus reducing forced outages,reactive maintenance and maintenance costs in general.
-It assures managers that equipment is being maintained
-It is easily understood and justified. However PM has some drawbacks which are stated below
- It is time consuming and resource intensive.
- It does not consider actual equipment condition when scheduling or performing the maintenance.
- It can cause problems in equipment in addition to solving them
RELIABILITY CENTERED MAINTENANCE:The goal is to provide the appropriate amount of maintenance at the right time to prevent forced outages while at the same time eliminating unnecessary maintenance
CONDITION BASED MAINTENANCE: This maintenance relies on knowing the condition of individual pieces of equipment.
HAPPY READING OF MY BLOG
-It is predictable,making budgeting,planning and resource levelling possible
- When properly practiced,it generally prevents most major problems,thus reducing forced outages,reactive maintenance and maintenance costs in general.
-It assures managers that equipment is being maintained
-It is easily understood and justified. However PM has some drawbacks which are stated below
- It is time consuming and resource intensive.
- It does not consider actual equipment condition when scheduling or performing the maintenance.
- It can cause problems in equipment in addition to solving them
RELIABILITY CENTERED MAINTENANCE:The goal is to provide the appropriate amount of maintenance at the right time to prevent forced outages while at the same time eliminating unnecessary maintenance
CONDITION BASED MAINTENANCE: This maintenance relies on knowing the condition of individual pieces of equipment.
HAPPY READING OF MY BLOG
Tuesday, August 30, 2011
express: GENERAL MAINTENANCE STRATEGIES FOR MECHANICAL EQUI...
express: GENERAL MAINTENANCE STRATEGIES FOR MECHANICAL EQUI...: Maintenance recommendations are based on industry standards and experience in Reclammation facilities.However equipment and situations vary ...
GENERAL MAINTENANCE STRATEGIES FOR MECHANICAL EQUIPMENTS
Maintenance recommendations are based on industry standards and experience in Reclammation facilities.However equipment and situations vary greatly and sound engineering and management judgement must be exercised when applying these recommendations.other sources of information must be consulted.
PREVENTIVE MAINTENANCE: the practice of maintaining equipment on a regular schedule based on elapsed time or meter readings.The aim of PM is to prevent maintenance problems or failures before they take place by following routine and comprehensive maintenance procedures.
PREVENTIVE MAINTENANCE: the practice of maintaining equipment on a regular schedule based on elapsed time or meter readings.The aim of PM is to prevent maintenance problems or failures before they take place by following routine and comprehensive maintenance procedures.
Friday, August 19, 2011
express: Check engine using a cell phone
express: Check engine using a cell phone: AutoMobile is a car diagnostic software for Symbian , Java and BlackBerry cell phones. It has a simple, user-friendly interface and it us...
express: How to make video calling
express: How to make video calling: On this page, we look at video calling - the technology used to make voice and video calls over the Internet. The idea of having video phone...
express: how to use mobile phone to detect human health con...
express: how to use mobile phone to detect human health con...: A new £5.7 million project being led by St George’s, University of London is developing self-test devices that can plug directly into mobile...
Tuesday, August 2, 2011
People interested in cheats
Latest mtn operamini cheats
IP: 010.199.212.002.
PORT:8080
HTTP:82.145.208.101
SOCKET:82.145.208.101
HOST:10.199.212.8
IP: 010.199.212.002.
PORT:8080
HTTP:82.145.208.101
SOCKET:82.145.208.101
HOST:10.199.212.8
Saturday, July 30, 2011
Glo Dstv mobile:For Glo subscribers
Multichoice has introduced DSTV Mobile to the Glo network. With this, all Glo subscribers with DSTV Mobile compatible mobile phones will now be able to enjoy their favorite DSTV channels while on the move. DSTV Mobile is based on Digital Video Broadcast-Handheld (DVB-H) a technology that allows the broadcast of digital terrestrial television and audio to any mobile phone with built-in DVB-H receiver. Access to DSTV Mobile is free until March 31, 2011. DSTV Mobile is available in Lagos, Abuja, Ibadan, Asaba, Onitsha, Kaduna, Enugu, Aba, Benin, and Port Harcourt. Hottest phone for DSTV Mobile is the Nokia 5330 Mobile TV Edition which goes for N28,000.
DSTV Mobile was formally only available to MTN subscribers. Now Glo and MTN subscribers in Nigeria can enjoy the service.
Here are channels available on DSTV mobile.
CNN
Super Sports 7
Super Sports Select
Super sports BLITZ
Channel O
Sound City Premium
Africa Magic
Africa Magic Hausa
Africa Magic Yoruba
NTA plus
Magic World
TBN
Cartoon Network
Read More about DSTV Mobile at the blog.
DSTV Mobile was formally only available to MTN subscribers. Now Glo and MTN subscribers in Nigeria can enjoy the service.
Here are channels available on DSTV mobile.
CNN
Super Sports 7
Super Sports Select
Super sports BLITZ
Channel O
Sound City Premium
Africa Magic
Africa Magic Hausa
Africa Magic Yoruba
NTA plus
Magic World
TBN
Cartoon Network
Read More about DSTV Mobile at the blog.
Friday, July 29, 2011
IT SOLUTIONS; How to get imei and mep code on blackberry phones.
You might need to know your IMEI number to generate your unlock code and sometimes even the MEP code might be asked. How to get those details from your BlackBerry handset ?
We provide solution with a very simple software that allow you to read your phone:
You can still use the old method to obtain your IMEI number directly from your phone:
We provide solution with a very simple software that allow you to read your phone:
- Run and install this software (file scanned – 100% spyware and virus free)
- Connect your BB handset to your computer using the original USB cable
- Run the Blackberry Logger/Reader and click “Read Blackberry Handset Info“
You can still use the old method to obtain your IMEI number directly from your phone:
- type *#06# into your mobile keypad
- OR
- From the Home screen: select Menu > Select Options > Select Status :Your IMEI will be located on the screen with the PIN and ESN numbers.
Wednesday, April 27, 2011
how to use mobile phone to detect human health conditions
A new £5.7 million project being led by St George’s, University of London is developing self-test devices that can plug directly into mobile phones and computers, immediately identifying infections. The project is called eSTI (electronic self testing instruments for STIs), and is being led by Dr Tariq Sadiq, senior lecturer and consultant physician in sexual health and HIV at St George’s, University of London. Most of the funding is coming from The Medical Research Council – and the UK Clinical Research Collaboration.
The UK has seen a 36 per cent rise in STIs from 2000 to 2009 – often blamed on the reluctance of the population to get diagnosed and the stigma of going to public health clinics – prompting the support of this project.
Researchers will use nanotechnology to create devices for testing multiple STIs, such as chlamydia and gonorrhea, similar to pregnancy test kits. These would be available in different settings, such as pharmacies and even vending machines, for users to add their samples and then plug into a computer or mobile phone.
It appears the technology will be aimed at phones that have the capability to connect to external devices and run mobile apps – smart phones such as the iPhone, Android devices, Blackberry, among others.
The UK has seen a 36 per cent rise in STIs from 2000 to 2009 – often blamed on the reluctance of the population to get diagnosed and the stigma of going to public health clinics – prompting the support of this project.
Researchers will use nanotechnology to create devices for testing multiple STIs, such as chlamydia and gonorrhea, similar to pregnancy test kits. These would be available in different settings, such as pharmacies and even vending machines, for users to add their samples and then plug into a computer or mobile phone.
It appears the technology will be aimed at phones that have the capability to connect to external devices and run mobile apps – smart phones such as the iPhone, Android devices, Blackberry, among others.
Sunday, April 24, 2011
How to make video calling
On this page, we look at video calling - the technology used to make voice and video calls over the Internet. The idea of having video phones in people's houses, or making video calls from mobile phones, is nothing new, but from 2006, there's a push to make house-to-voice video calling more popular - the magic ingredient being broadband Internet, which now makes person-to-person home videocalling practical.
Video phone calling was first trialled a few years back over standard phone lines, but these lacked the bandwidth to support stable video calls. Now that more and more homes have moved over to higher-bandwidth broadband services, video calling is now possible in higher quality, and users of services such as MSN Messenger have been able to use webcams to do two-way video for a couple of years now.
In an attempt to make video calling easier and more accessible, BT has brought out a couple of videophones, to encourage less computer-savvy people to make use of video-over-Internet. To use these devices, you need to sign up to the free BT Broadband Talk service (free with BT Total Broadband). With BT Broadband Talk, video calls via your broadband connection can be made between two BT Videophones, a BT Videophone and a Softphone (on a PC with a webcam), or two Softphones used with webcams. If you're looking for advice on getting or using a videophone, hopefully we can help.
The Videophone 1000 and Videophone 2000 both make use of a Broadband connection for voice and video calls over the Internet, and BT are encouraging users to make use of their voice/video-ready BT Home Hub with BT's Videophones and BT Broadband Talk. These phones use something called Hi-dS (standing for High definition Sound) to achieve decent voice quality over the 'net, and in tests we did for our podcast, the quality of voice calls over BT Broadband Talk were pretty impressive (Take a listen to our tests in Frequencycast Show #08) .
If you're interested, take a look at our reviews...
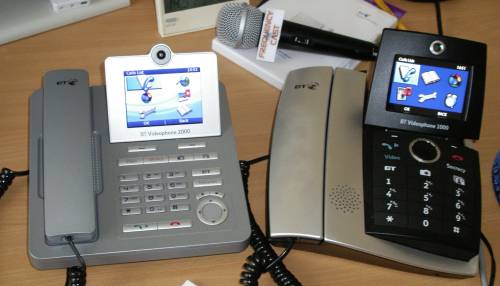
BT's Videophone 2000 and Videophone 1000
Softphone accessories can be found at shop.bt.com
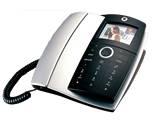
In an attempt to make video calling easier and more accessible, BT has brought out a couple of videophones, to encourage less computer-savvy people to make use of video-over-Internet. To use these devices, you need to sign up to the free BT Broadband Talk service (free with BT Total Broadband). With BT Broadband Talk, video calls via your broadband connection can be made between two BT Videophones, a BT Videophone and a Softphone (on a PC with a webcam), or two Softphones used with webcams. If you're looking for advice on getting or using a videophone, hopefully we can help.
![]() ![]() Listen to the show online, or download it to your MP3 player. Listen to Show 08 | What is FrequencyCast? | Add us to iTunes |
Videophones
In 2006, BT brought out two dedicated videophones that can be used to make video phone calls over broadband. We've been lucky enough to get hold of these handsets for review, and have been generally pleased with the results. The two handsets are listed below.The Videophone 1000 and Videophone 2000 both make use of a Broadband connection for voice and video calls over the Internet, and BT are encouraging users to make use of their voice/video-ready BT Home Hub with BT's Videophones and BT Broadband Talk. These phones use something called Hi-dS (standing for High definition Sound) to achieve decent voice quality over the 'net, and in tests we did for our podcast, the quality of voice calls over BT Broadband Talk were pretty impressive (Take a listen to our tests in Frequencycast Show #08) .
If you're interested, take a look at our reviews...
The BT Videophone 1000 This supports voice and video , and is connected to Broadband Advice via an ethernet cable and a compatible router.
| ![]() |
The BT Videophone 2000 As well as video calling, this videophone has a basic web browser, and has a few extra media features not supported on the more basic Videophone 1000. It can also connect to the Internet wirelessly with wi-fi.
| ![]() |
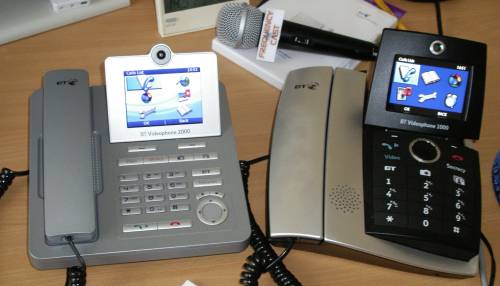
BT's Videophone 2000 and Videophone 1000
BT Softphone
This is a free bit of software from BT, and if you've even used a PC Instant Messenger application such as MSN or Yahoo, you'll be familiar with the concept. The app is downloaded and installed onto your PC, and runs in the background. You can use it to initiate a voice or video call, using a microphone and/or webcam connected to your PC. The Softphone application can communicate with other PCs using Softphone software, or can make voice/video calls to phones such as the Videophone 1000 or Videophone 2000. You can also use the service for cheap voice calls over the Internet using BT Broadband Talk.Softphone accessories can be found at shop.bt.com
Wednesday, April 6, 2011
Check engine using a cell phone
AutoMobile is a car diagnostic software for Symbian, Java and BlackBerry cell phones. It has a simple, user-friendly interface and it uses a Bluetooth OBD adapter that connects to the vehicle's standard OBD2 (On-Board Diagnostic) connector. It's wireless, so no cables are needed!
AutoMobile 3.1 is now available! If you purchased any of the previous versions, request the upgrade from support@automobile3.com.
AutoMobile 3.1 is now available! If you purchased any of the previous versions, request the upgrade from support@automobile3.com.
Sunday, April 3, 2011
punch-Angry mob set INEC office ablaze in kaduna
Government Area of Kaduna State, on Saturday set ablaze the INEC office in the area after chasing away the members of staff of the commission.
Many of the voters who claimed to have arrived at the various polling stations in the area as early as 6.30am, decided to go to the INEC office to verify the reasons for the delay in the arrival of election officers and voting materials.
An eyewitness, who pleaded anonymity, told our correspondent that tempers flared and a violent protest ensued when there was no INEC official on hand to explain the situation to the demonstrators who subsequently set the INEC office in the area ablaze.
Unspecified number of persons were also said to have been injured. Several calls put through by our correspondent to the INEC Acting Public Affairs Officer, Mrs. Fatima Bande, were not answered.
Also in Zaria, irate youths numbering about 500 beat up and stripped naked a man suspected to be in possession of ballot papers at a polling unit in Durumin Maigarke. The police unsuccessfully tried to rescue the suspect. The youths tore his dress and used it to tie his hands behind him.
The Chairman of the Conference of Nigerian Political Parties and second republic governor of Kaduna State, Alhaji Balarabe Musa, alleged that the postponement of the election was a ploy by the ruling Peoples Democratic Party to secure an extension of the tenure of its current political office holders.
Musa alleged that since the 1999 constitution allowed the government in power to remain in office till the conduct of the next election, the PDP government was taking every step to truncate the April elections with the ultimate aim of extending its stay in office.
He said, “What this means is that the PDP is going to have a third term in office. The 1999 constitution says that when elections fail to hold, the governors and the President should remain in power till such a time when elections are conducted.
“By May 29, the President and the governors will continue and you know that the National Assembly will not allow them to continue without them and so, they will go and amend the constitution to take care of them.”
Many of the voters who claimed to have arrived at the various polling stations in the area as early as 6.30am, decided to go to the INEC office to verify the reasons for the delay in the arrival of election officers and voting materials.
An eyewitness, who pleaded anonymity, told our correspondent that tempers flared and a violent protest ensued when there was no INEC official on hand to explain the situation to the demonstrators who subsequently set the INEC office in the area ablaze.
Unspecified number of persons were also said to have been injured. Several calls put through by our correspondent to the INEC Acting Public Affairs Officer, Mrs. Fatima Bande, were not answered.
Also in Zaria, irate youths numbering about 500 beat up and stripped naked a man suspected to be in possession of ballot papers at a polling unit in Durumin Maigarke. The police unsuccessfully tried to rescue the suspect. The youths tore his dress and used it to tie his hands behind him.
The Chairman of the Conference of Nigerian Political Parties and second republic governor of Kaduna State, Alhaji Balarabe Musa, alleged that the postponement of the election was a ploy by the ruling Peoples Democratic Party to secure an extension of the tenure of its current political office holders.
Musa alleged that since the 1999 constitution allowed the government in power to remain in office till the conduct of the next election, the PDP government was taking every step to truncate the April elections with the ultimate aim of extending its stay in office.
He said, “What this means is that the PDP is going to have a third term in office. The 1999 constitution says that when elections fail to hold, the governors and the President should remain in power till such a time when elections are conducted.
“By May 29, the President and the governors will continue and you know that the National Assembly will not allow them to continue without them and so, they will go and amend the constitution to take care of them.”
Saturday, April 2, 2011
Tuesday, February 15, 2011
Subscribe to:
Posts (Atom)